Magnetics Division - Global Equipment Mktg Inc.
Self Cleaning Magnets
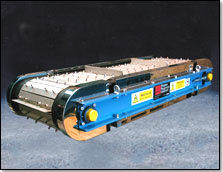
The Type 'K' Self-Cleaning Magnet, the #1 selling Permanent Self-Cleaning Magnet in North America, are standard on portable and stationary crushing, shredding, grinding, screening and recycling plants, with thousands in operation throughout the world. Recycling operations include MRFs, C & D, crushed concrete/asphalt, scrap wood, crushed glass, scrap tires and other solid waste applications. While these are just some of the uses for these magnets, they are operating in other industries with great success.
The Self-Cleaning Recycling Magnets are Permanent Magnets using the latest and highest grade of materials suitable for this type system. When compared to electro magnets, no electrical source is required for the magnet, it is considerably lighter in weight, has a lower profile, is virtually maintenance free and less expensive to purchase, install and operate. In many applications the Type 'K' have many advantages over an electro magnet.
Previous solutions to separation of ferrous and tramp iron, be it rebar, wire, screening, drill steel, loader teeth, sledgehammers, nails, tin cans or steel heading, from the material being processed has been to employ belt-pickers or metal detectors. While both are expensive alternatives to the Type 'K' Self-Cleaning Magnets, the metal detector will also continuously shut down the process if too much ferrous is present.
Companies that use our Type "K" Self-Cleaning Magnetic Separators have reported back that they have recovered the original cost in as little as two months due to reduction in manpower, minimal production stoppages, higher percentage of reclaimed scrap and upgraded better quality end product.
The magnet block enclosed in this system is powerful, computer designed, and mounted in a heavy-duty steel frame. The magnet is traversed with a heavy-duty vulcanized cleated belt running on two crowned pulleys and driven by either an electric or hydraulic motor, depending on the application. The entire system is designed for durability and is able to operate in the harshest environments. Stainless steel magnet and belt guards on both sides of the magnet are standard and run the full length for safety of workers and protection of the system.
These magnet systems are normally suspended by their eyebolts, over the conveyor at a specific distance, called the "working gap" - the distance from the magnet face to the bottom of the processed material. Normally suspended from a goal post, A-frame or 4-poster type steel structure, they are available for both crossbelt (perpendicular to the conveyor processing the material) and in-line applications (same direction as the conveyor and over the head pulley). As tramp ferrous metals pass underneath the magnet and become attracted to the face of the magnet, the cleated belt moves the metals clear of the conveyor burden transporting it out of the magnetic field, discharging it away from the conveyor.
Click here for more Product Details from
Magnetics Division - Global Equipment Mktg Inc....