Metallurgical Technologies, Inc.
Metallurgical Failure Analysis
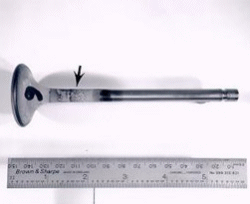
We are experts in metallurgical forensic failure analysis and engineering. Our metallurgical engineers analyze and determine the root cause of failure and make recommendations to prevent future recurrence. Through a careful extensive forensic examination and analysis of: background information, service environment, fracture surfaces, and mechanical and chemical properties of the component; the pieces of the puzzle are fit together in a conclusive manner and a root cause of failure is identified.
Metals typically fail by: fatigue, corrosion, overload, embrittlement, wear, metal creep, fretting, deformation, erosion, hydrogen damage and cracking, and stress corrosion cracking. A complete forensic failure investigation can identify which of these mechanisms or what combination of mechanisms contributed to the component failure. We can also determine whether manufacturing, processing or design issues contributed to or caused the failure.
The following are a few of the wide variety of industries from which we serve. Click on the links below to see several examples of forensic engineering investigations and metallurgical failure analysis that we have provided.
The information presented is copyrighted and may not be downloaded, reused, modified, distributed, or otherwise used without the express written permission of Metallurgical Technologies, Inc. P.A.
Our Forensic Process
A typical forensic metallurgical failure analysis includes the following eight steps:
- Collect failed component background information and service history.
- Perform a visual examination of failed and related components in the as-failed condition. Perform low magnification examinations using a stereomicroscope to locate critical areas for further analyses or testing. Take dimensional measurements as necessary.
- Analyze the fracture or degraded surfaces utilizing a Scanning Electron Microscope (SEM) at high magnification.
- Using the SEM, determine the failure mode and origin/initiation site. Investigate the initiation site for unusual conditions or contributing factors. Identify and characterize the failure mechanism (fatigue, embrittlement, overload, type of corrosion, etc.) Investigate for unusual stress risers.
- Select, prepare, examine and analyze the cross-section microstructure in the region of failure/fracture initiation. Analyze conditions of manufacturing reflected in microstructure and investigate potential flawed conditions. Investigate material quality and heat treat conditions.
- Perform a chemical composition analysis of the failed component (alloy and impurities), and coatings or platings.
- Perform mechanical and other testing (hardness, strength, toughness, etc.).
- Analyze all gathered evidence and test results to formulate an engineering opinion and conclusion.
Through a careful extensive forensic examination and evaluation of the evidence gathered from the above analysis, the pieces of the puzzle are fit together in a conclusive manner and a root cause of failure is identified.
All evidence and forensic failure analysis results are photographically documented and presented in a report, which interprets and explains each finding in a clear and concise format. We also provide: reports of evidence in support of resolving insurance claims, expert witness testimony, and litigation support in product liability and accident cases.
Click here for more Product Details from
Metallurgical Technologies, Inc....